Everyone can agree that 2020 was a completely unprecedented year for the global economy. The entire supply chain was disrupted and all businesses, workplaces, and employers had to pivot their operations in ways previously unknown.
While prior to 2020 the idea of working at home was mostly relegated to freelance contractors, 2020 catapulted nearly the entire working population into that category. Where business owners found themselves struggling was in the management of machines and employees.
Now, the world economy is starting to recover, but business owners are still grappling with some of the same questions.
How can machine shops engage employees who remain on a work-at-home basis until they can get their vaccine? How can machines be remotely controlled to provide better throughput, workflow, and lights-out management?
These are the questions businesses everywhere need to tackle—and answer—if they are to remain competitive in a post-pandemic world.
Though businesses are primarily looking to return to “business as usual,” the manufacturing world has been forever changed by the events of 2020. That means, as much as business owners want “normal” to return, they face a “new normal” instead. While virtual management may not be as necessary as it was when nearly everyone was working from home in the pandemic days of mid-2020, the adjustments made are going to become part of regular business activities, including the ability to manage machines and employees virtually.
Without virtual management capabilities in place, businesses might just get left behind by those that continue to incorporate these capabilities into their business structure for increased output and profitability.
Invest in Top-Tier CNC Shopfloor Management Software
Better virtual management will always start with digitalizing the shop floor, placing machines and employees on a virtual network that provides instant feedback to both in terms of shop processes, throughput, and machine performance.
The best software that will tie machines and employees together is a suite that allows for the simultaneous and instant management, analysis, and optimization of machine tools. With these three items in place, managers and shop employees can access real-time data, adjust workloads, and gain insight from automatic digital analysis to optimize workflow and machine downtime.
All CNC machine shops recognize that downtime is one of the most significant factors in reducing profitability and employee productivity. When a machine is down, the machine’s operator is then taken offline to focus on troubleshooting issues with the machine. Whether it is past due for maintenance, a tool got out of alignment, or the unit needs to be reconfigured, the operator is taken away from their regular job to troubleshoot, and the machine’s workload is halted until the problem is solved.
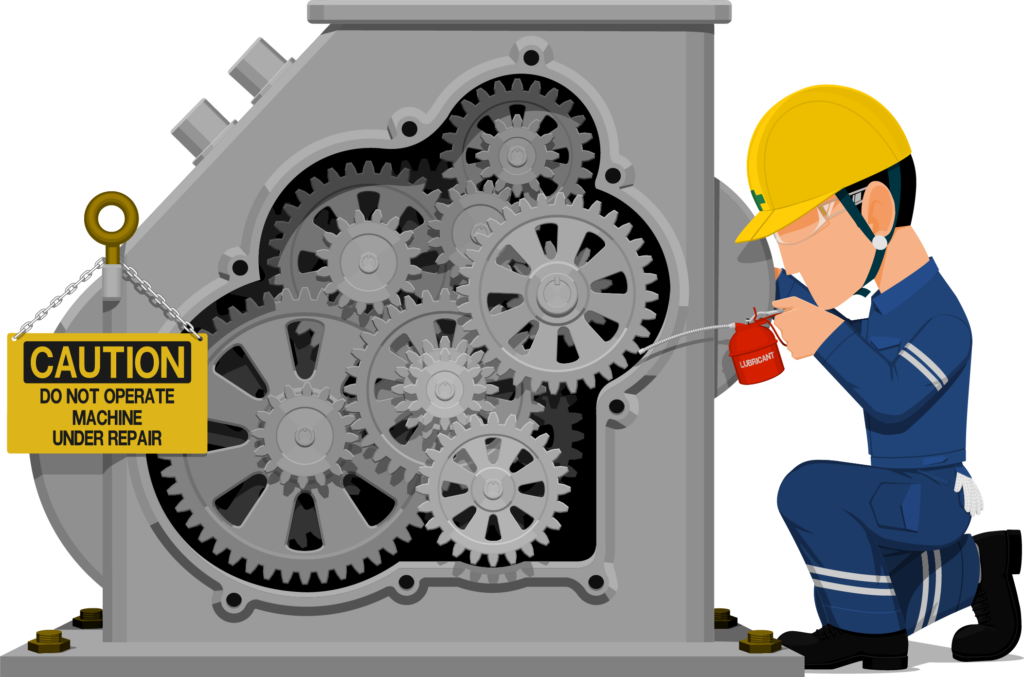
With the digitalization of the shop floor, unexpected downtime can be dramatically reduced, unexpected problems minimized, and workflow and production boosted. Software that automatically feeds analytic data to machine controllers empowers employees to make critical decisions that save the shop floor, and the company, time and money.
Place More Data Into the Hands of Employees
When a limited number of employees are running the shop floor and managers are left to remotely work with them, empowerment for in-the-moment decision-making is key. The pre-pandemic shop floor ran very differently, with different operators able to run questions by the supervising manager by waving them over to ask a question.
Today’s employees are not only reduced in number, but also their supervising manager might not even be on-site for part of the day. What these employees need is data at their fingertips with guided analysis to make decisions along with the kind of instant communication that allows their supervisors to “OK” their choices.
Remote management software that links CNC machines together can simultaneously provide data to machine controllers and supervisors. With integrated communication software between workers, managers can access the same data set their employees see. Rather than emails or phone calls back and forth, with the right communication software, managers can approve or recommend actions based on real-time data.
Remote management and real-time data give employees the ability to be proactive in suggesting a course of action while providing managers the ability to preside over these decision-making opportunities.
With this kind of data access and communication, employees are given the power to make decisions with the safety net of having managers virtually by their side to provide further information, insight, and opportunities for learning.
Digitalize the Entire Shop Floor Process From Start to Finish
Digitalization only works to its full capacity if the entire process, from product design and machine concept to product execution and machine servicing, is digitalized. While it can be argued that any amount of digitalization is better than none at all, only partially digitalizing the shop floor will more often than not leave employees lacking data, information, and necessary analytics for accurate decision-making. Managers and machine operators alike need the maximum amount of data possible to make decisions effectively.
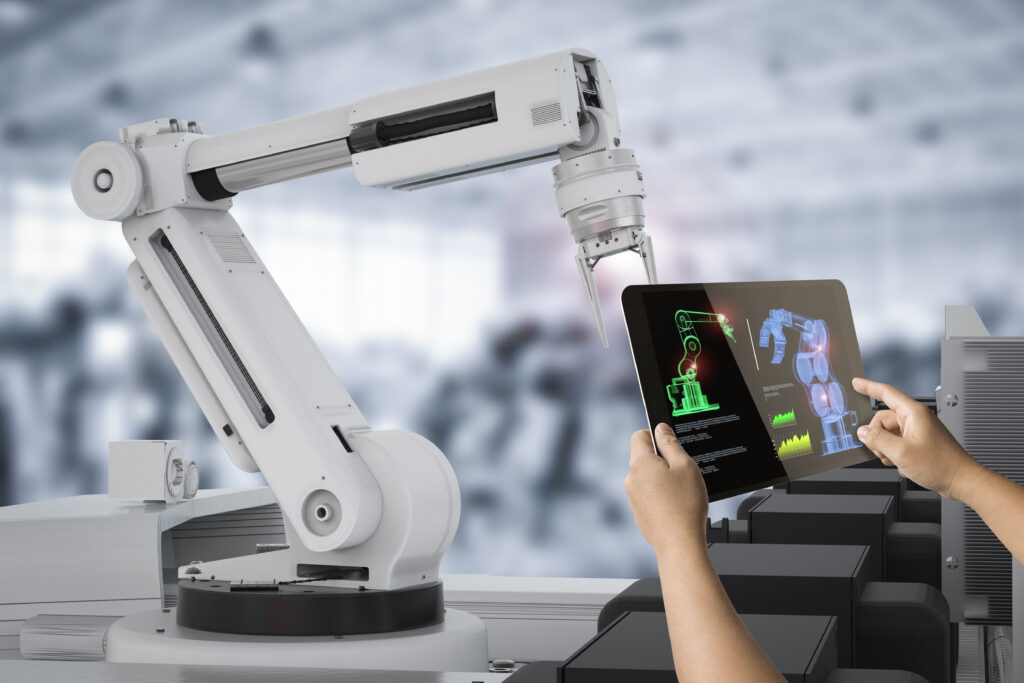
For machine operators, accessing the entire value chain is critical. They need access to product development, production planning, production timing, required output, machine tool life, and the minute set of data that informs them what the machine can handle.
By accessing this kind of data, the ability for optimization grows exponentially. The more a shop floor can be optimized for workflow, downtime, and throughput, the more shop productivity and industry competitiveness can be increased.
Incorporate Cloud-Based IoT Software
Digitalization is only as good as the ability to access data and remotely interact with it. If a shop switches machines over to a digital process but then proceeds to place the data on an internal server, the digital information is only as good as their on-site ability to process it.
If nothing else, 2020 showed the world that data must be remotely accessed. The answer, of course, is to incorporate cloud-based IoT software when the shop floor is digitalized.
When machine data streams instantly to the cloud, managers can access and effectively manage shop floor employees regardless of whether they’re in the same state or a different country. Data is key to management and shop floor data must be hosted somewhere other than an internal server. Cloud-based data should be remotely accessible by all parties who are involved in the management and decision-making processes for the shop floor. With remotely accessible data, all employees will have the ability to optimize machine processes, production rates, scheduled downtime, and total shop floor efficiency.